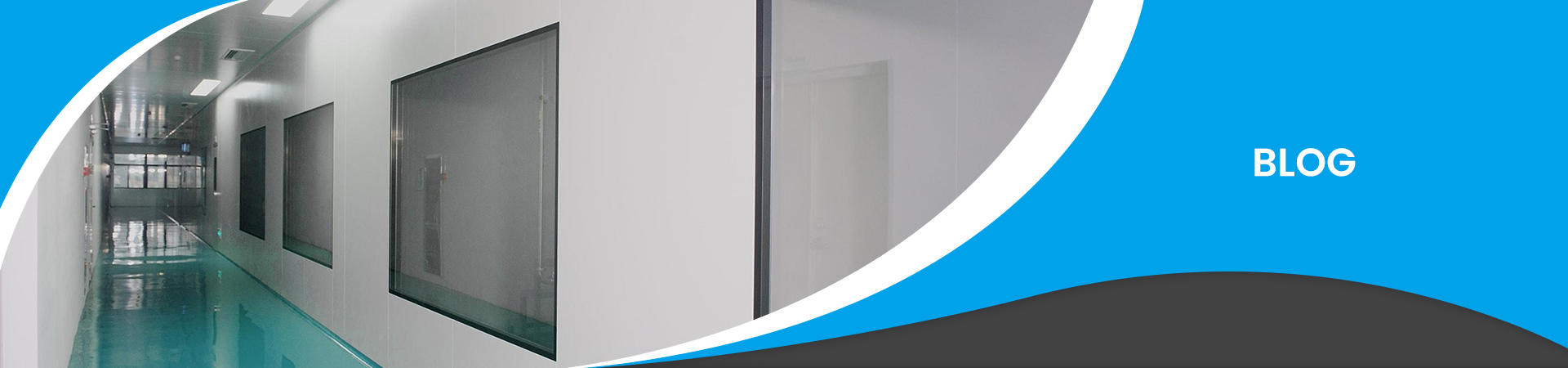
Why You Should Use a Great Pharmaceutical Door Manufacturer
- By:ren
- 2022-11-04
- 29
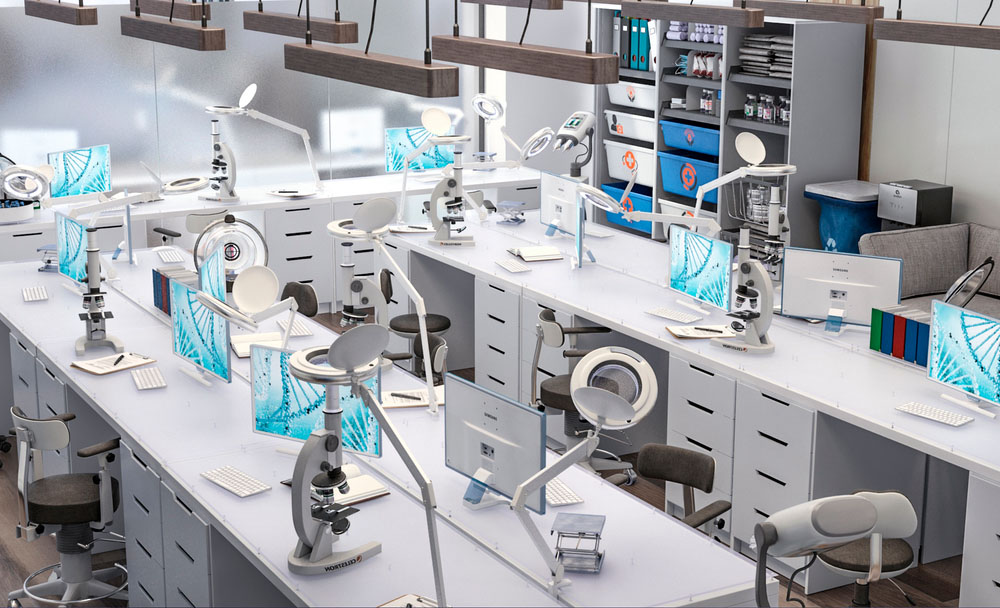
It’s no secret that the pharmaceutical industry is highly regulated, and any business looking to enter that market needs to be aware of all the guidelines and rules involved. If you’re thinking of creating a custom door for a pharmaceutical company, there are several important factors to keep in mind before diving in. If you’re considering manufacturing doors for these types of businesses, it’s critical that you understand exactly what is required by regulatory agencies such as the Food and Drug Administration (FDA) to mitigate risk and remain compliant. The scope of this article applies primarily to manufacturers creating new products or services within the pharmaceutical space; however, many of these regulations also apply to vendors selling finished goods or raw materials used in their production.
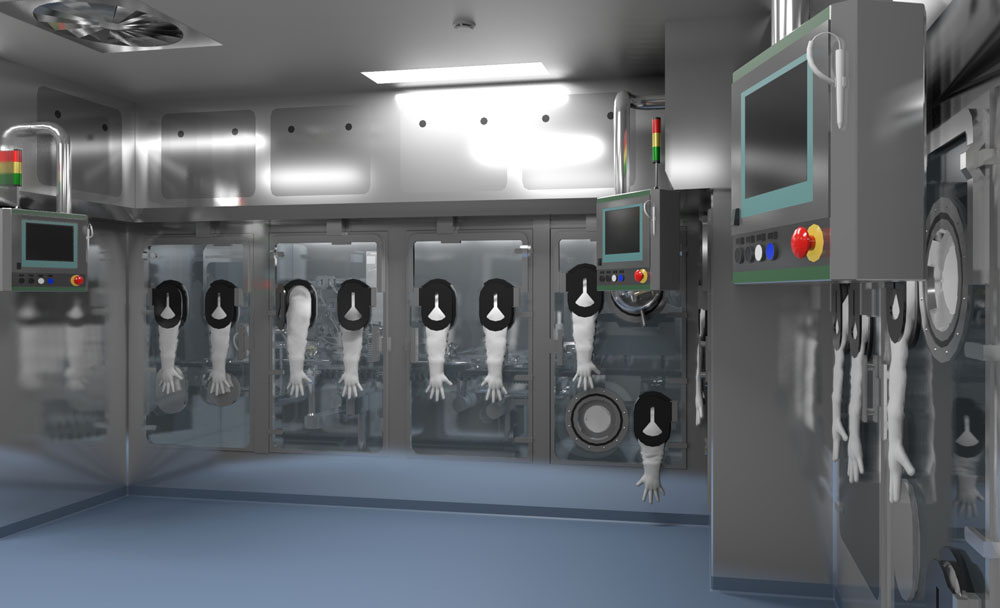
What are Pharmaceutical Door Manufacturer?
If you’re new to the pharmaceutical industry and manufacturing doors, you might be wondering, “What are Pharmaceutical Door Manufacturer?” Essentially, these are MDPE (medium density polyethylene) doors used to enclose pharmaceutical manufacturing and R&D spaces. The MDPE material is an FDA-approved resin that meets quality and testing standards regarding microbiological contamination and other health, safety, and security considerations. For pharmaceutical companies, doors play a critical role in maintaining a safe manufacturing environment. Doors not only help limit the spread of contaminants, but they also help prevent personnel from carrying pathogens from one area to another. In short, doors act as barriers to help prevent cross-contamination and diversion of controlled substances.
Why are they Important?
Diversion and theft of controlled substances is a real threat for pharmaceutical companies and regulatory agencies. As such, all controlled substances must be safeguarded to prevent theft, misuse, and diversion. The only way to do this is to ensure that all aspects of production — from procurement of raw materials to the end sale of finished goods — occur under the supervision of trained staff. What this means is that the entire supply chain must be monitored, tracked, and accounted for; otherwise, it is much easier to divert materials and/or product. The primary concern when it comes to manufacturing pharmaceutical products is that contamination and cross-contamination that could lead to product recalls. If a single door or piece of equipment were found to be contaminated and was subsequently used in the production of other items, those items could be contaminated as well.
What are the FDA’s current requirements for pharmaceutical door manufacturing?
As mentioned above, the primary concern with manufacturing pharmaceutical doors is contamination and cross-contamination. Over the past several years, the FDA has made several adjustments to its standard requirements for door manufacturing and material selection in an effort to reduce the risk of contamination and cross-contamination. As of October 19, 2018, the FDA’s current recommendations for materials and manufacturing processes are as follows: > Doors and frames must be manufactured with MDPE plastic. > Doors must have a self-lathing frame and be positive pressure. > Doors must meet minimum specifications for air leakage: - Air leakage rate of 1 cubic foot per minute at 100 Pascals (0.01 CFM at 100 Pa) - Air leakage rate at 0.02 CFM at 100 Pa > Airflow must be controlled and monitored with a minimum of two indicators. > Door seals must be inspected for defects on a regular basis (at a minimum, weekly). > Raw materials must be purchased from a certified manufacturer with a valid GMP certification.
Create a Diversion Control Plan (DCP)
The first step in creating a DCP is to select a suitable location for production. You’ll also want to consider factors such as distance to raw materials and access to transportation. When it comes to building design and construction, you’ll need to follow strict guidelines for airflow and positive pressure, which includes installing positive-pressure (PP) doors along with air curtains and/or doors with air filters. You’ll also need to follow strict guidelines regarding the selection and use of materials, including both construction elements and raw materials. For example, you’ll need to select a single-wall construction for piping and ductwork, with the exception of steam, water, and hydrocarbon gas lines. You’ll also need to choose a material that is non-reactive to chemicals being processed in the facility. Finally, you’ll need to perform regular maintenance and inspections of all equipment to ensure it is in good working order. Your maintenance schedule should include cleaning and decontamination as needed.
Establish Effective Quality Controls (eQC)
As with the creation of a DCP, you’ll want to follow strict guidelines for the selection of raw materials to be processed in your facility. You’ll also need to establish Quality Control (QC) procedures and perform regular inspections to ensure the equipment is in good working order. You’ll also need to follow strict guidelines for storage, including the use of chemicals with proper labels and signage where applicable. Finally, you’ll need to perform regular audits of your facility and its operations. Your audits should include both internal operations (e.g., production, storage, and transportation) and external operations (e.g., customer service and shipping operations). Your audits should also include a review of the certifications your facility holds.
Food and Drug Facility Finding (FDFF)
As you begin to work with contractors and vendors, you’ll need to confirm that each has appropriate certification for work performed on your site (e.g., Public Health, Fire, and Safety Authority (PHFSA) certification for electrical wiring and plumbing). You’ll also want to confirm that each vendor has a valid FDA registration. To do this, you’ll need to complete a Food and Drug Facility Finding (FDFF) form for each vendor. The FDFF form requires you to provide details about the vendor, including the type of product being sold or provided and the amount of revenue your company expects to generate. The form also requires you to provide information about the facility where the vendor will perform work, including the location of the building and the type of work that will take place there. Once you’ve completed the form, you’ll need to submit it to the FDA and wait for approval. The FDA typically responds to FDFF requests within 30 days, although it may take longer if your request is part of a larger backlog.
Confirm Pharmaceutical Door Manufacturer Process Steps
As you begin production, you’ll want to confirm that all equipment and procedures meet regulatory requirements. To do this, you’ll need to conduct regular inspections and audits of equipment and procedures. For example, you’ll need to ensure that all cleaning and decontamination procedures are followed and documented. You’ll also want to confirm that equipment is properly handled, maintained, and stored when not in use. You’ll also want to confirm that all raw materials meet regulatory requirements and are properly tracked through the manufacturing process. This includes confirming that suppliers have valid GMP certificates and have been vetted to ensure they are safe and reliable.
Final Words: The Importance of Confirming Manufacturing Processes
As you can see, there are many important factors to consider when Pharmaceutical Door Manufacturer pharmaceutical doors. From selecting appropriate raw materials to confirming that the manufacturing process is following regulatory guidelines, there are many different areas to focus on. This is why it is so important that pharmaceutical companies work with reputable door manufacturers who are knowledgeable about the regulatory requirements and can confirm that their manufacturing process is following those guidelines. If a company does not follow these guidelines, it can lead to negative consequences for the business, including product recalls, facility shutdowns, and/or fines from regulatory agencies.
-
Cleanroom Glass Windows Are The Key to Maintaining a Clean Environment
-
Top Aluminium Profile Manufacturers in China: Leading the Global Market
-
The Evolution of Air Tight Sliding Doors
-
AHU Aluminium Profile: A Comprehensive Guide
-
The Importance of Choosing the Right Cleanroom Door in Vietnam
-
The Benefits of Hospital Automatic Doors: Enhancing Efficiency and Safety
-
The Best Bathroom Door Manufacturers - Unlocking Endless Possibilities!
-
Unlock the Possibilities with AJ Manufacturing Doors
-
Make a Statement with Manufactured Home Interior Doors!
-
what is aluminum profile? Aluminum Profiles for Your Home is the best option
-
Next-Gen Medical Cleanroom Access: Introducing the Cleanroom Steel Door Solution
-
Linear Bar Grille Air Conditioning Diffuser with 0° Angle Blades for Perfect Airflow
-
The Sleek and Efficient Linear Slot Diffuser for Air Vent
-
Double-Swing Glass Doors - Modern Laboratory Cleanroom Doors
-
Superior Aluminium Glass Swing Door - Pharmaceutical Cleanroom Door
-
E-ZONG Leads the Way in China's Medical Lead Protection Doors: Innovation for Safety and Efficiency
-
E-ZONG: Leading the Suppliers of Glass Airtight Automatic Doors for Safer, Cleaner Spaces
-
How Wall Air-Tight Swing Doors Ensure Clean Environments With Secure & Silent
-
Seamless Automatic Cleanroom Sliding Doors: Smooth, Safe, and Hygienic Solutions
-
Elegant & Durable: Premium Swing Door Protection for Hospitals
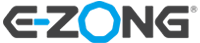
Guangzhou Yizhong Aluminum Industry Co., Ltd.
We are always providing our customers with reliable products and considerate services.
We are always providing our customers with reliable products and considerate services.
Speak Your Mind